The Industry Leader in Dust Containment Solutions
Control Dust. Eliminate Downtime. Protect Your People.
Reduce regulatory risks, improve site safety, and keep your conveyor system running efficiently with Flexco’s industry-leading dust containment solutions for mining, aggregates, and bulk material handling.
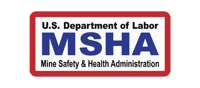
Keep Your Workers Safe & Avoid Excess Fines
with MSHA’s Latest Policies
MSHA’s updated regulations on Respirable Crystalline Silica (RCS) dust exposure reduce the permissible exposure limit (PEL) to 50 μg/m³ over an 8-hour shift and introduces stricter monitoring and action limits. Tangible engineering controls are now required to reduce airborne dust, as respirators or rotating employees are no longer acceptable solutions. Non-compliance puts your employees at risk of long-term health complications, and your facility at risk of facing heavy fines.
Coal mines are required to comply by August 18, 2025, and MNM mines by June 17, 2026. Learn more by visiting www.Flexco.com or contacting your local Flexco representative today.
🛠️ Defeat Dust with Flexco 🛠️
Dust is more than just a nuisance—it’s a costly and dangerous byproduct of inefficient conveyor systems. Excess airborne dust can lead to MSHA violations, increased maintenance costs, health hazards for workers, and reduced equipment lifespan. Mining facilities that fail to address dust containment risk unexpected shutdowns, regulatory fines, and lost profits.
At Flexco, we provide dust prevention solutions that help operations reduce emissions, protect workers, and maintain compliance. Our conveyor belt skirting, impact beds, and cleaning systems are designed to eliminate dust at the source—keeping your material where it belongs and your site running smoothly.
Site Walkthrough Request Form
Are you facing uncertainty throughout your conveying process? Is your bottom-line suffering from increasingly costly downtime incidents? Allow Flexco to help with a site walkthrough!
Featured Application Stories
Explore real-world success stories on dust containment and see how operations have minimized dust exposure, improved compliance, and enhanced conveyor efficiency with proven solutions.
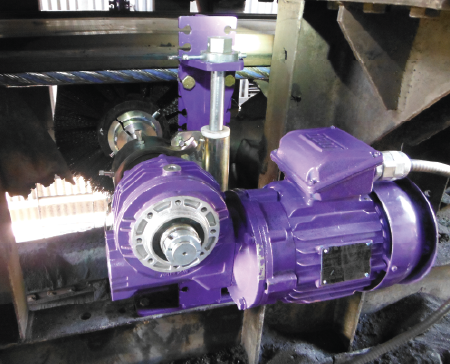
Belt Cleaning Systems
Flexco Cleaners Tackle Extreme Carryback for Auto Glass Manufacturer
An auto glass manufacturer struggled with excessive carryback, leading to dust buildup, costly cleanup efforts, and a $3,000 annual air-compressor expense. Operators resorted to wheelbarrows under return rollers to catch falling debris, adding $10,000 in cleanup costs.
Flexco recommended replacing polyurethane cleaners with carbide-tipped solutions, installing an HV Precleaner, FMS Secondary Cleaner with V-Tips, and a Motorized Brush Cleaner driven by a hold-down roller.
The result? 85% less carryback, reduced cleanup costs, and a significant drop in air-compressor use. The innovative approach impressed plant managers and optimized long-term belt performance.
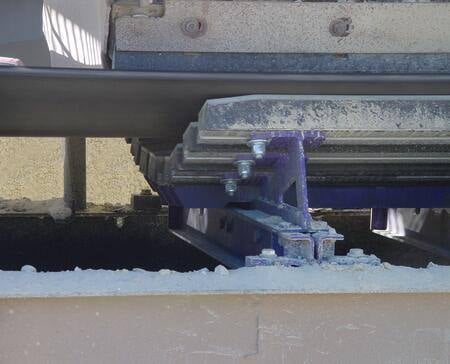
Impact Beds & Skirting Systems
Gravel Plant Learns the Importance of Calculating Load Zone Transition Distances
A Texas gravel plant installed a Flexco DRX™ 3000 Impact Bed and Enclosed Skirting System to reduce spillage and dust, but the seal failed within a week. Confused by the issue, the maintenance team called in a Flexco expert for an inspection.
The issue? Incorrect transition distance and belt elevation. The tail pulley was too high, causing the belt to lift out of the trough and break the seal.
By lowering the tail pulley to align with the center idler cans, the system achieved proper sealing, eliminating dust and material loss for a more efficient operation.
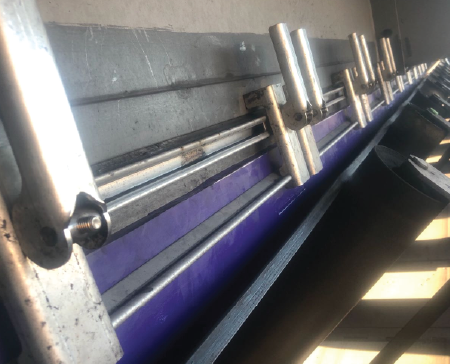
Skirting Systems
Flexco Dual Seal Polyurethane Skirting Reduces Clean-Up, Protects Belt
A European infrastructure project was struggling with excessive spillage and rapid skirting wear on a high-angle conveyor. Their existing skirting deteriorated every 2-3 months, leading to frequent replacements and increased cleanup labor.
During a routine visit, Flexco’s team recommended Flexco Dual Seal Polyurethane Skirting, designed for longer wear life and improved containment. Its dual-contact design prevents material loss and dust emissions while allowing easy adjustments.
Since installation, the new skirting has lasted three times longer, reduced cleanup needs, and helped protect the belt from damage, keeping the project running smoothly.
The Hidden Cost of Dust:
Why Prevention Matters
Unchecked conveyor belt sag leads to more than just material spillage—it creates costly inefficiencies and on-site hazards like:
- Lost Productivity – Excess dust and spillage require constant cleanup, pulling workers away from essential tasks and slowing operations.
- Equipment Damage – Sagging belts accelerate wear, leading to belt mistracking, idler failure, and pulley damage.
- Compliance & Safety Risks – Airborne dust exposes workers to respiratory hazards and increases the risk of MSHA fines.
Proactively addressing belt sag with proper support solutions keeps material contained, extends equipment life, and protects both workers and profits.
Featured Solutions for Dust Containment
Flexco’s dust mitigation solutions help you limit dust expulsion at your conveyor transfer points, improving operational efficiency, ensuring compliance with industry regulatory guidelines, and creating a safer workplace for your team.
Belt Support Bar
Stabilize Your Belt & Minimize Dust
The Belt Support Bar minimizes belt sag at conveyor transfer points, ensuring a smoother flow of materials and reducing the opportunity for dust to escape. By creating a more stable belt surface, the bar enhances the sealing efficiency of skirting systems and limits dust generation.
CBS Belt Cleaner
Cleaner Belts = Cleaner Air
The CBS Continuous Blade Secondary Cleaner provides another area of protection by obliterating carryback as a dust source. Its continuous blade design ensures consistent pressure for superior cleaning.
Impact Beds
Protect Your Belt & Prevent Spillage
Impact Beds absorb the shock of material loading at transfer points, preventing belt damage and material spillage that contribute to dust generation. By stabilizing your belt, these beds help to contain material and maintain a cleaner environment.
Skirting Systems
Seal the Edge. Stop the Dust.
Skirting Systems create a reliable seal along conveyor belts, containing material and reducing the escape of dust particles. Flexco’s long-life urethane skirting is a durable solution for a safer and cleaner work environment.
Our Heavy-Duty Industry Experts
When you partner with Flexco, you gain access to the industry's most dedicated team of industry experts.
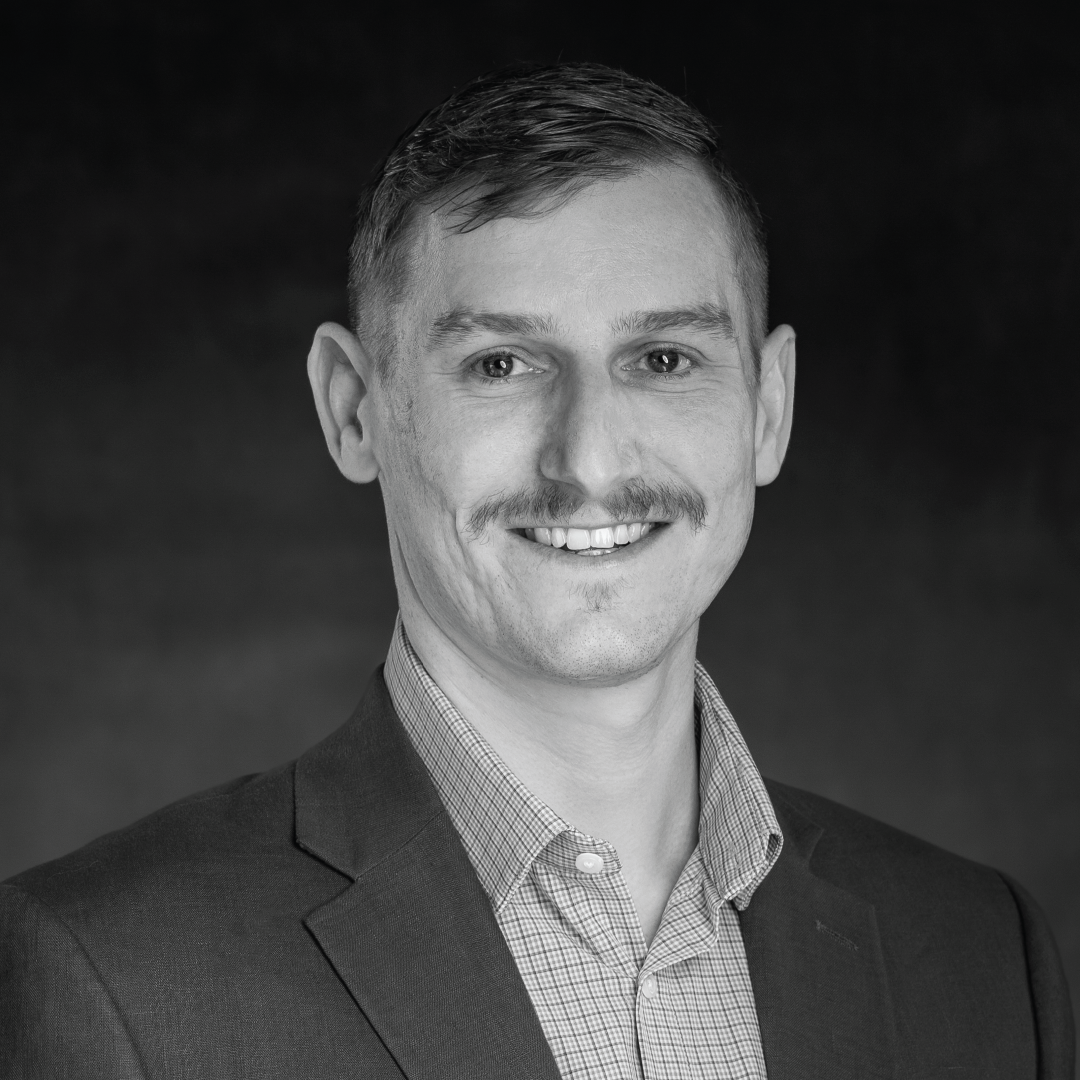
Travis Vliem
Product Manager
Vliem is responsible for the Flexco Elevate™ IoT platform – researching and designing business capabilities and go-to-market strategies, implementing and driving adoption of the program, assisting in researching and developing new sensing and monitoring systems, and capturing and evaluating the voice of the customer.
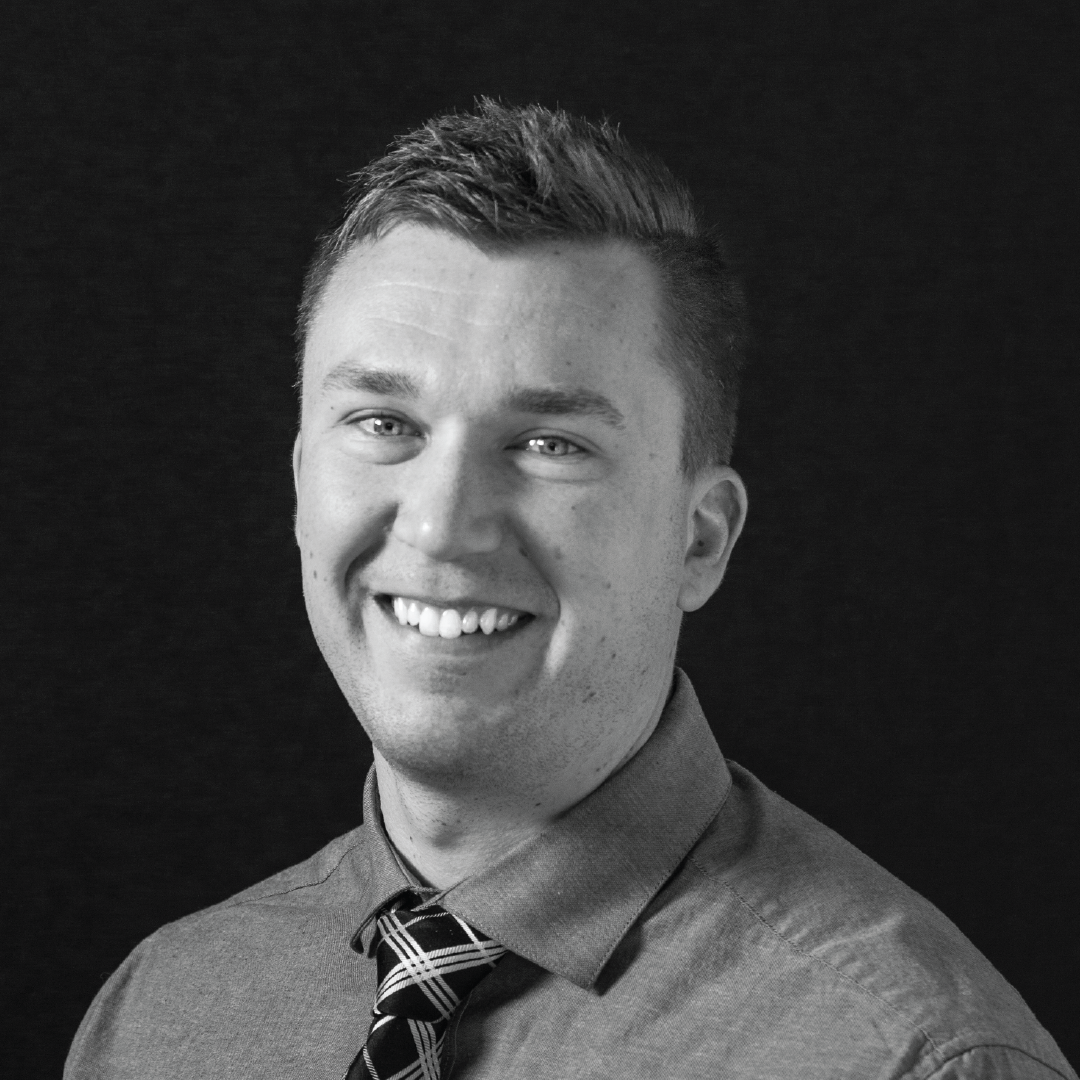
Franklin Moore
Product Manager
In the role of Product Manager, Moore is responsible for the market strategy for Flexco’s line of mechanical belt fasteners, the FXC™ Steel Cord Belt Fastening System, and the Minet Lacing Technology product line in the U.S., Canada, and Mexico, which includes the Super-Screw® line of fasteners and Fix’N Go® Rip Repair.
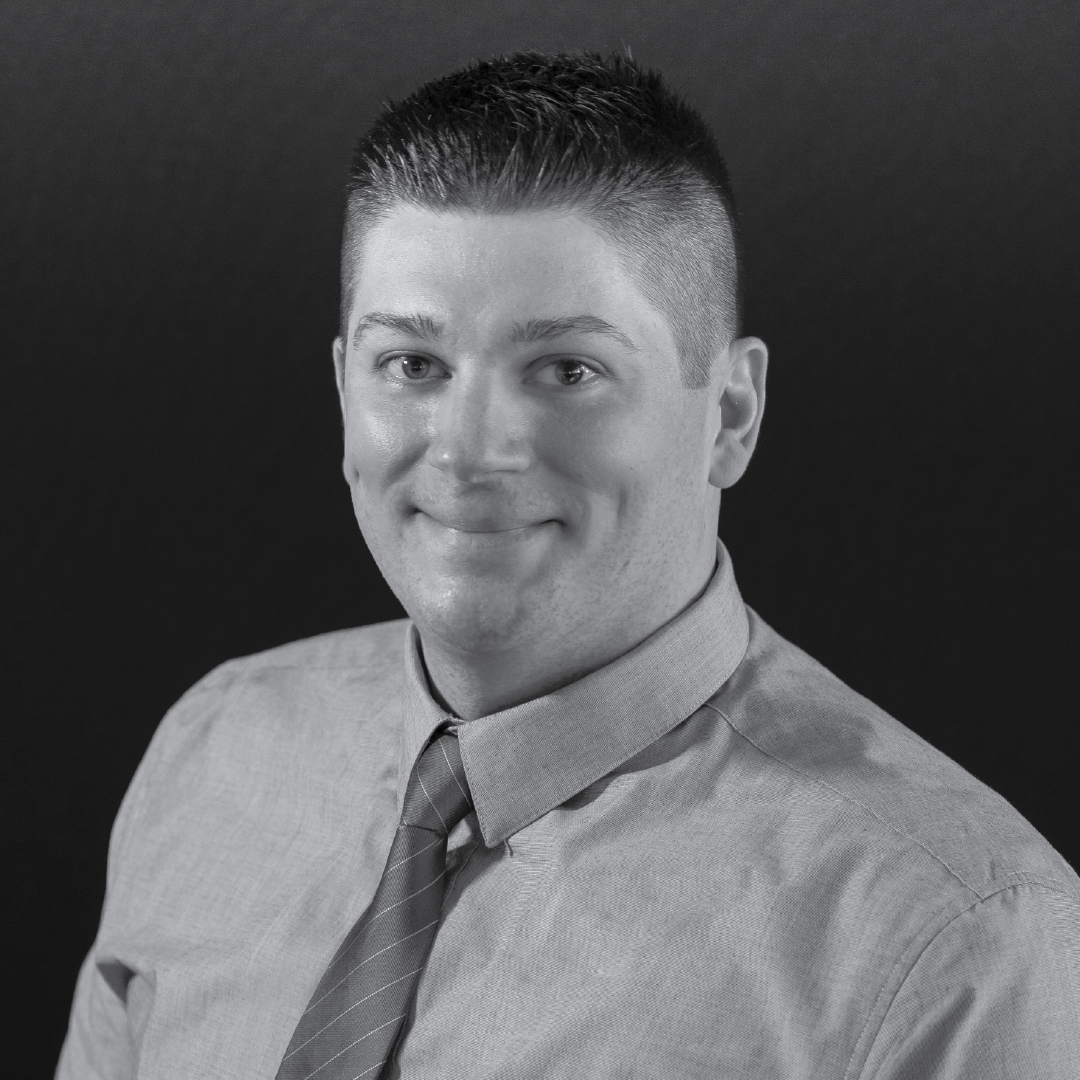
Kevin Fales
Product Manager
In the role of Product Manager, Fales manages the Belt Conveyor Product line, providing strategic guidance for the global business unit. This includes identifying product development opportunities and working with global engineering resources to create new product concepts and enhance existing products.
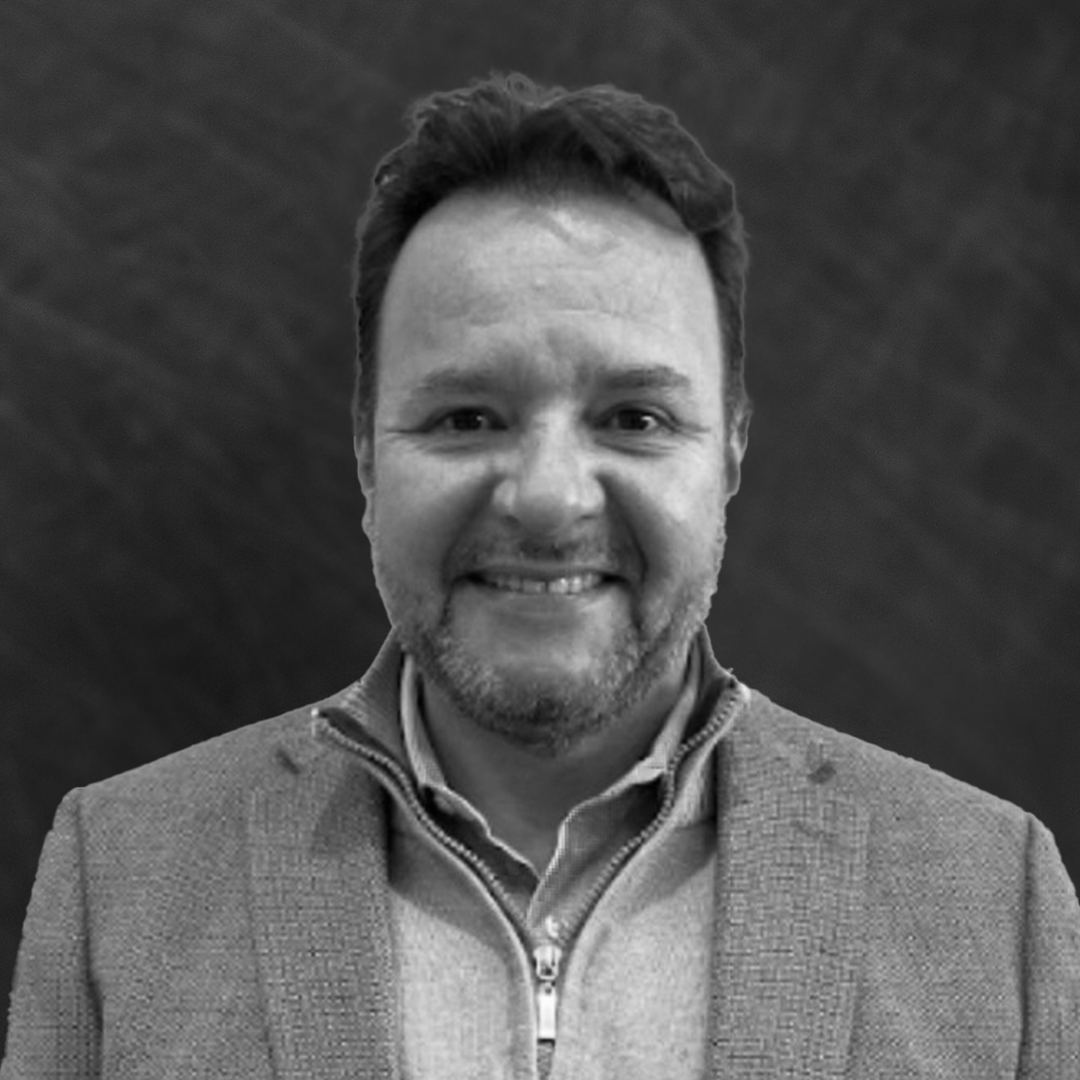
Rafael Peraza
Inudstry Manager
As Heavy-Duty Industry Manager – Cement/Aggregate, Rafael Peraza leads Flexco’s efforts to deliver targeted solutions for the cement and aggregate industries. With a strong background in engineering and field operations, Rafael partners with customers to identify key challenges and ensure Flexco’s products, support, and strategy are aligned to solve them.
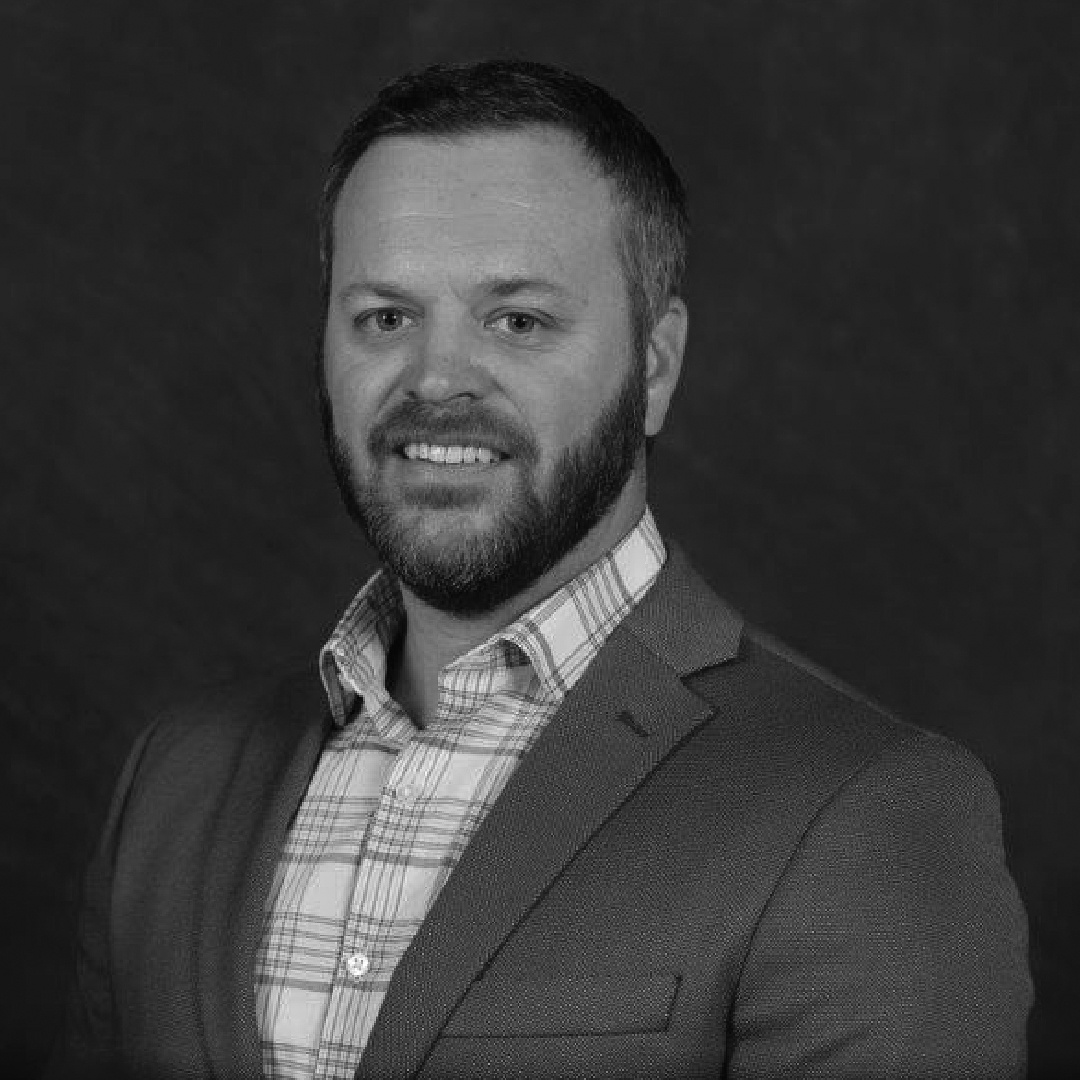
Aaron Wilson
Accounts Manager
In the role of Strategic Accounts Manager, Wilson supports our vision of maximizing belt conveyor productivity for our global strategic account customers and channel partners, all while helping to create an environment where talented employees of heavy-duty belt conveyor systems can better thrive & succeed on the job.
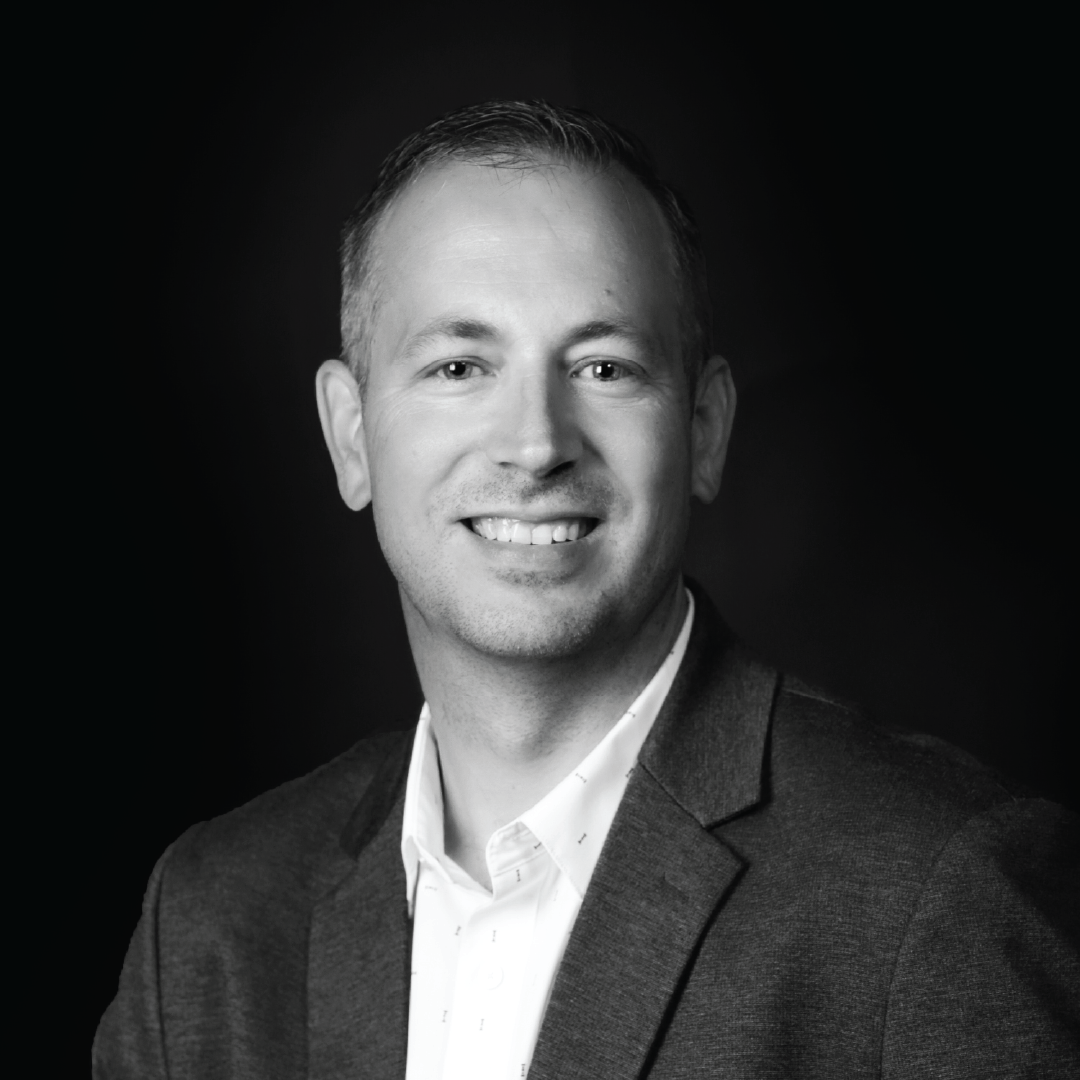
Ryan Grevenstuk
Industry Manager
As Heavy-Duty Industry Manager – Hard Rock, Ryan Grevenstuk works to align Flexco’s product strategy with the specific needs of hard rock mining operations. His role focuses on enabling product activation, identifying growth opportunities, and ensuring that Flexco’s solutions deliver measurable value for customers in the field.